In the last update I mentioned the load of tubes that arrived in the mail. Unfortunately my main three suppliers are out of the drop outs I need and my back up is in Taipei.
Not to be dismayed I continue to keep myself busy and move along with what I can do at the moment. In addition to lacing up some wheels, I busied myself with prep work for the next build.
I do most of my design work in my noggin, then finish up and pull miter angles and lengths off of a full sized drawing. This also gives me a visual to double check things like pedal to fender clearance, etc. Here is a pick of the current build's drawing.
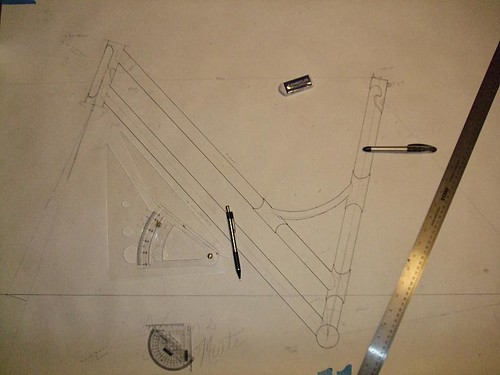
This is for a 700c rambler. The terms city bike and hybrid have started to pigeon hole a bit (hybrid maybe more then a little bit). I'm calling my mulit-use bikes "ramblers", custom designed for
your application (not just a mix of road and mountain like aspects). In this case I am matching the handling geometry of a race frame with the position and fit of a 74' Schwinn Suburban. This will be for a rider re-couping from a wrist injury that just couldn't get into pushing around 40+ lbs of American pig-iron, but loved her mixte fit.
This frame will use a Dedacciai Uno tube set and be a fillet/ bi-laminate constructed bicycle. Essentially, bi-laminate means that steel sleeves will be brazed on the outside of the thin walled tubes to act as an external butte to support the loads of intersecting tubes. Sort of like open faced lugs. In the drawing, these can be seen at the head tube, top tube, and 3 on the seat tube. Any place a butted end will be brazed to a thin section, there will be a laminated sleeve to help distribute the load.
Most bicycle tubing is measured in mm. The seat tube in this case is 28.6mm in diameter, but only .6mm thick in the thin part of the wall. 28.6mm is about 1 1/8". 1 1/4" 4130 with a wall thickness of .058" slip fits over a 28.6mm tube with just enough room to sweat in some silver. But who wants to put a hog .058" (1.47mm) sleeve onto a .6mm tube?
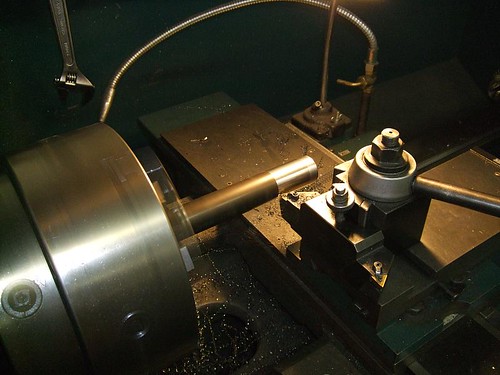
To balance out the wall thicknesses I turned down the 4130 stock on the lathe to about .7mm. Sticking this on will more then double the tubes wall thickness with a negligible weight penalty, will help mitigate heat distortion from brazing, and will look totally bad ass with some subtlety carved embellishment.
I'll try to do a better job of taking in-progress pics and blogging about this build. Stay tuned for the next installment!